MacLean-Fogg Internship
Mechanical Engineering Intern
Newberry, South Carolina
SKILLS
Lean Manufacturing
SolidWorks Assembly
Designing for Manufacture and Assembly
GD&T

CHALLENGE
Design a mechanism that will reduce defects from the drilling process in composite beams.

OVERVIEW
During my 2017 summer internship with Maclean-Fogg, I was tasked with reducing defects in composite beams due problems with the CNC drill press. This system had to handle large composite beams with vertical and horizontal drill holes. The holes from the original drill bed had aesthetic problems from the drilling process that caused customers to return the beams. I designed a new modified drill bed to fix these aesthetic issues from conception to final approval. Working through the design process using in a real-world environment with real-world repercussions for the first time was challenging, fulfilling, and exciting as an engineer. My use of lean concepts from this project will prove valuable in the future.
Composite Beam
Supported Area= No Defects

Un-Supported Area= Defects
Drill
Bit
Foam
MY CONTRIBUTIONS
Prototype
I began with a proof of concept mock-up to demonstrate the feasibility of this concept. I designed back support block in SolidWorks that supported the exit drill hole to prevent defects. After milling the support block, I assembled a mock-up with two pieces of 8020 (T-slotted aluminum) and fixed the support block using set screws. This mock-up confirmed that this concept was viable for full-scale implementation.

Final Design
The biggest design hurdle was discovering the method of clamping the supports in place. I used two toggle clamps for the vertical support because it was an easy mechanism for operators to use and could withstand the vibrations from the CNC drill. The horizontal slider used four set screws that pushed against the T-slotted aluminum to remain in place. Working through the hurdles throughout this design process presented me an opportunity to thoroughly practice my design skills and apply mechanical concepts learned from class.
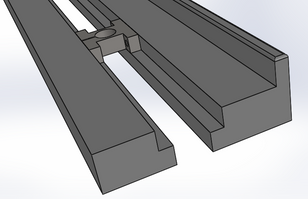


IMPACT & CONCLUSION
This entire design process presented me with various challenges, but ultimately, I successfully designed a system reduced defects and streamlined the process for drill operators. Although I didn't see this design through full implementation because of time constraints, the final design was approved and implemented. The biggest takeaway from this project is to never assume any aspect of the design is suitable for use. Design is an iterative process that requires constant modifications to your project. Modeling on SolidWorks is great from prototyping, but until prototypes are tested, it is hard to predict what problems your prototype will encounter. Once the problems are recognized, appropriate modifications can then be made to the design.

